VDA6.3 过程审核中五大工具的使用问题...
资料来源:中国国际标准管理研究院 点击:
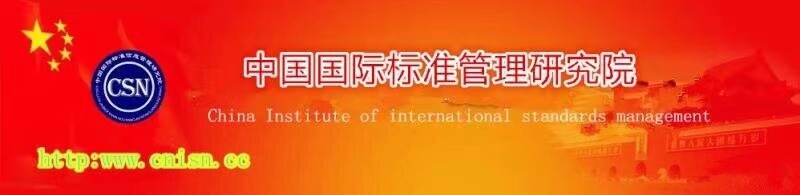
VDA6.3 过程审核中五大工具的使用问题.....
本期我们来看VDA6.3 过程审核中五大工具在供应商端的主要问题......
汽车行业五大工具包括APQP&CP,PPAP,FMEA,MSA,SPC.
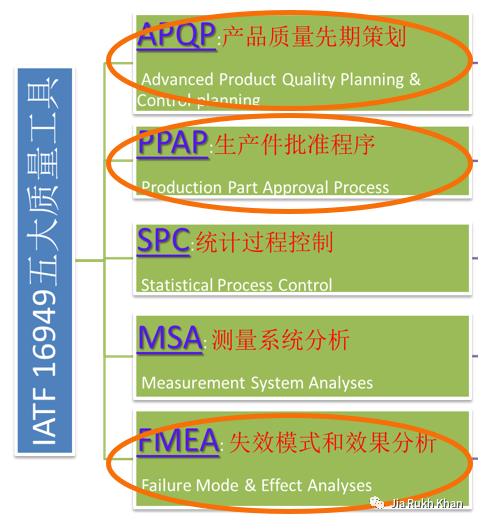
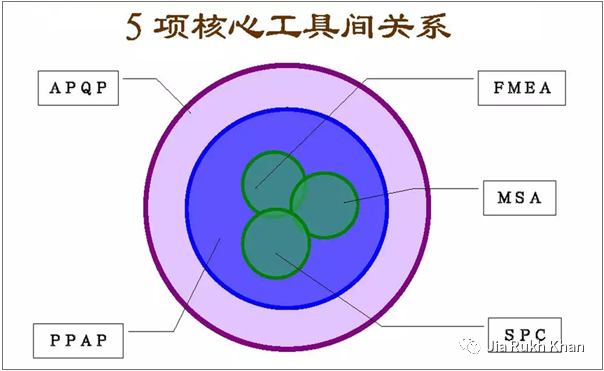
说到这理,肯定有人会问,你讲的不是VDA6.3 吗,怎么又和汽车行业5大工具扯上了,没错,VDA6.3 作为VDA QMC 出具的关于过程审核的标准,其所有条款中都没有明确说使用以上工具,但是在在以下条款中有所描述。
客观地讲,VDA6.3 的脱颖而出,本身就是为了弥补和细化美系AIAG 五大工具的短板,所以对于非汽车行业(工程机械行业)来说,使用VDA6.3 审核供应商,本身就是建立在IATF16949+AIAG五大工具+客户的特殊要求上的,只不过这里的SPC.MSA目前还处在基础的应用中,比如SPC仅停留在对Y进行管控,未主动针对X进行管控,且子组的取样量也不足以支撑得到有效的可信服的数据,或者不管数据正态性如何,也不管公差是不是单边公差,直接套用公式计算等种种错误的打开方式,而MSA更是只用%GR&R,不用%P/T,或者取样有意无意的错误等等,本次不在此赘述。
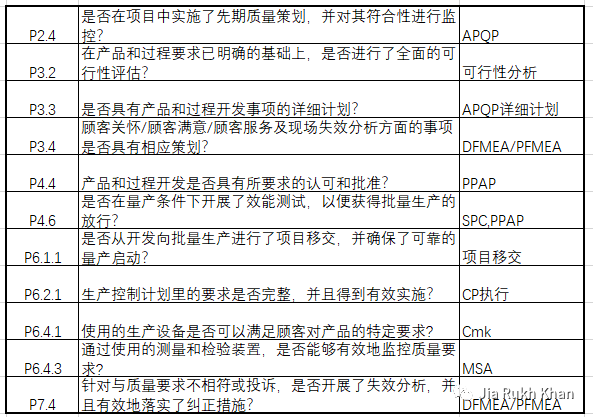
当前工程机械供应商端,在执行VDA6.3 过程审核时存在以下主要问题:
1.APQP :
Ø1. 无APQP 或部分缺失。
Ø2.普遍缺少APQP 第2阶段产品设计和开发.
Ø3.缺少阶段评审报告。
Ø4. 80%缺少项目向生产的交接,🐅头🐍尾
Ø5.执行层面出现问题.
2.FMEA:
Ø1. 80%的供应商FMEA对FE/FM /FC的识别不到位,尤其是针对客户端的失效模式。
Ø2. 90%的供应商缺少DFMEA。
Ø3. 60% FMEA中的改进和预防措施描述没有可执行性,比如加强检验加强工人培训。
Ø4. 70% FMEA 中识别到的FM.FC,FE,PA,CA未向CP传递。
Ø5. 出现8D质量问题后,未更新FMEA.
Ø6.PFMEA小组未涵盖生产班组长及一线操作工.
3.MSA
Ø量检具未识别完成,未进行有效性和溯源性验证。
Ø量检具缺失或者分辨率不够。
Ø做MSA 时,员工有意无意地取样错误。
Ø只看%GR&R,不看%P/T。
Ø使用Excel计算结果,未使用专业的minitab,JMP,Q-das等软件进行操作,不能分析交互作用。
Ø未进行Cg,Cgk检测(量具的准确性和精确性)
Ø对于外观件,不进行一致性比率或其他验证
4.SPC
Ø有意无意的取样错误
Ø不管啥样数据,都直接套用休哈特常规控制图,有的客户也是只要供应商提交数据,根本不管数据的来源是否有效,寻求一种心理安慰而已。
Ø使用Excel强套结果,未使用专业的minitab,JMP,Q-das等软件进行操作,不满足SPC使用前提。
ØMSA 未做,就直接使用SPC。
Ø只有初始过程能力,批产时不再监控。
Ø控制数据来自于办公室,而不是生产工位。
Ø不做变异源分析SOV,不做DOE,直接进行SPC。
5.PPAP
Ø不理解做PPAP 的目的,不愿意做PPAP。
ØPPAP样本数量不足,无法验证供应商的过程能力,Cpk/Ppk的置信区间过大,没有参考意义。
ØPPAP完成后未向生产传递
Ø未包含二级供应商的PPAP过程
Ø未固化生产设备,测量设备,方式方法等5M1E。
Ø….
关于以上这些主要的不符合项,可能有的看官目前还不能深刻理解其中的水深水浅,但确确实实在企业的质量管理工作中切实存在,并且被一些人员坚持使用,无知不可怕,可怕的是无知而不自知,后续有机会将逐一分析。
学习,永不止步......
上一篇:质量管理体系的起点在哪里?
下一篇:“现代财务管理实战高级研修班